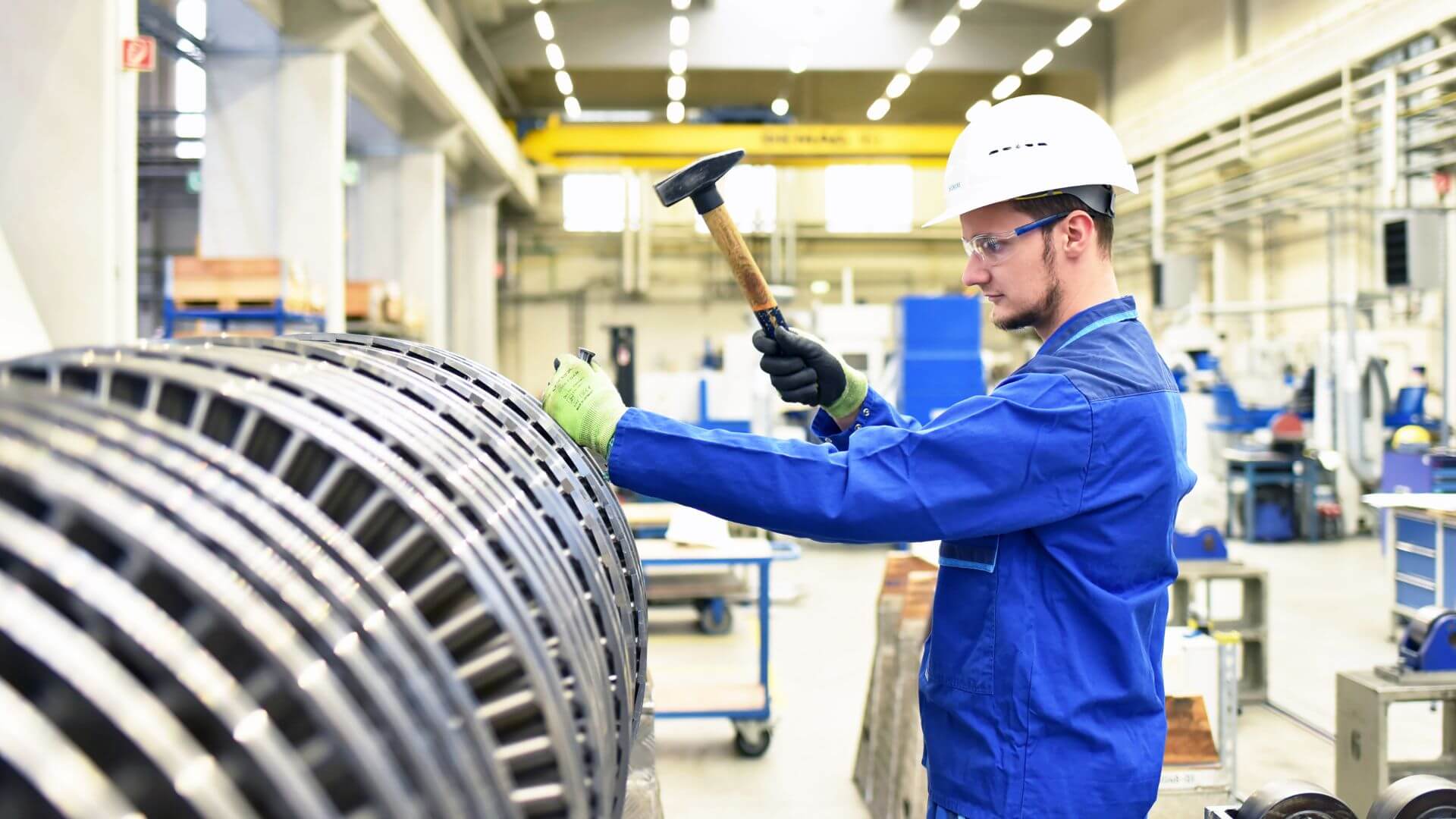
Background
A premier Original Equipment Manufacturer (OEM) of Medium & Small sized Steam turbines sector required a better decision support solution with ready availability of real time business & operational information. The existing business information reporting processes with a number of manual steps delayed availability of information and hampered the organization’s ability to respond with speed to dynamic needs of the market.
Problem Statement
The OEM's manual reporting system, while robust, faced challenges in meeting the evolving needs of dynamic market environments. Limitations in providing real-time insights and the inherent complexities of manual data handling presented ready opportunities for improvements. Recognizing these aspects, the company proactively sought to innovate and improve its decision support solutions to enable its decision-making processes and market responsiveness.
In seeking a more advanced decision support system, the OEM aimed to harness real-time business and operational data to refine their strategic and operational decisions. This vision was about elevating the entire decision-making ecosystem. The objective was to empower the organization with immediate insights and actionable intelligence, ensuring that every decision was informed by the latest data, thereby significantly enhancing responsiveness and agility in a competitive market landscape.
Solution
The client approached us to develop a comprehensive solution to overhaul their reporting mechanism. This process began with a thorough discovery phase to pinpoint the client's specific challenges and pain points with their existing manual reporting methods. We followed a holistic approach, covering various departments including Manufacturing, Marketing, Sales, and Human Resources, to ensure a comprehensive upgrade in reporting capabilities.
Our solution involved a strategic overhaul of the client's reporting system through the implementation of Microsoft Power BI. By implementing Microsoft Power BI, we enabled automated, dynamic reporting across all departments. The solution focused on:
- Integrating disparate data sources for a unified view of operations.
- Developing customized dashboards for real-time monitoring and insights.
- Automating report generation to reduce manual effort and errors.
- Providing training to staff for maximizing the benefits of Power BI.
The implementation of Power BI enabled dynamic, automated reporting that could handle complex data analyses such as product turnover, order tracking, cash flow, cost monitoring, order booking trends, inquiry feedback, warranty tracking, and HR insights. This shift not only improved internal efficiencies but also aligned the client with contemporary industry trends and best practices.
Outcome
The adoption of Power BI transformed the OEM's reporting and data analytics capabilities. The new system led to:
- Significant reductions in reporting time and manual errors.
- Enhanced decision-making through real-time data insights.
- Improved operational efficiency and market responsiveness.
- Strengthened competitive positioning in the industry, paving the way for sustained growth and innovation.
This case study exemplifies the power of digital transformation in overcoming traditional operational challenges and driving business success in a competitive landscape.